We believe in being consistent with our deliveries. This means that we are always on time and able to work for your business needs, no matter what they may be.
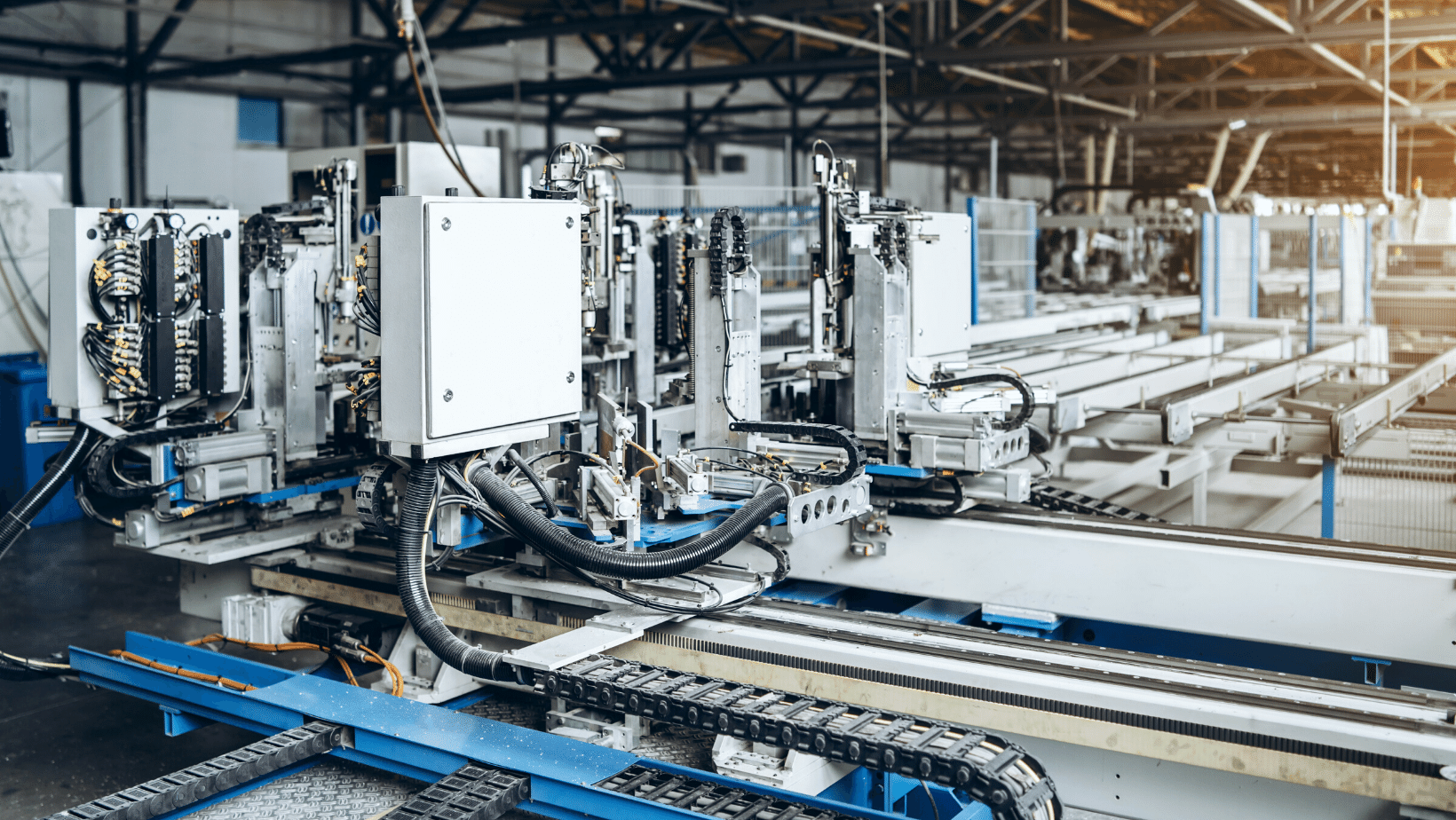
As automation technology advances, so must the machines that support it. In order to keep up with the latest trends in industrial automation and the Internet of Things (IoT), machine designers need to employ advanced design principles and software capabilities.
Using reliable software tools and efficient design methods can help you create machines that are ready for the future of industrial automation.
By automating your manufacturing processes, you can improve your productivity and efficiency while reducing costs. With the right technology in place, you can make your plant more agile and responsive to changing market conditions.
Keep reading to learn more about how modern automated machine principles can help you stay ahead of the curve in today's rapidly evolving industrial landscape.
- How do automated machines work?
- What are the benefits of automated machines?
- What are the most common problems in using automated machines?
- What are some examples of automated machine design?
- Automation, Machine Design, and IIoT
How do automated machines work?
Advanced automation machines use a combination of different systems such as PLCs, scanners and sensors to help them function properly. The assembly line that makes cars in a factory is an example of advanced end-to-end automation. In this line, the car chassis is moved from station to station where workers install different components such as seats or motors. This would be very difficult for a human to do, which is why it's done by robots working in unison with each other.
The use of lasers can also be used on advanced automation machines as a method of detecting different types of quality issues. For example, lasers can be used to assess the surface quality of discs produced by automated equipment.
A PLC is a piece of equipment (semiconductors) that contains both hardware and software. The way it works is the PLC receives commands from either an automated system or a human operator, and then it sends those commands to its actuators, which make things happen. One example would be an automated machine that uses PLCs to run different parts through a process, like a cell manufacturing system.
PLCs are a type of automation technology that can be used to control equipment on an automated machine. They have been around for many years and allow manufacturers to easily implement safety features before automating those processes.
Machine sensors are used to collect data, identify problems, and send signals for corrective action. Sensors can be placed on different machine parts or components that need to be monitored in order to protect workers and machinery. For example, sensors can be used on robotic arms to ensure they don't come into contact with hazardous voltage or pinch workers' hands as they move around the factory floor.
What are the benefits of automated machines?
By designing your machines so that they can be easily automated, you will see improvements in many areas of the manufacturing process. Some benefits include:
1- Increases productivity
Manufacturers can achieve greater levels of output per shift.
2- Minimizes product defects
Automating the machine means there is no need for manual inspections or interventions while it's running, meaning that errors are greatly reduced.
3- Reduces labor costs
A machine designed for automation can allow you to cut down on labor costs by reducing the need for human intervention while it's running.
4- Increases agility
An automated manufacturing cell allows you to adjust your manufacturing process on the fly. If you have a change in demand, you can increase your production levels quickly.
5- Increases flexibility
An automated manufacturing cell allows you to perform multiple tasks at the same time, making it easy for you to switch from one product or task to another.
What are the most common problems in using automated machines?
While designing a machine for automation is a daunting task, there are potential pitfalls that can stand in the way.
1- Not planning for future growth
An automated manufacturing cell is only as good as the equipment that's placed into it. If you are not committed to growing your operations, increasing output, or increasing efficiency by adding more machines, you will run out of room quickly.
2- Lack of connectivity
It's important that your automation equipment is able to communicate well with all of the other machines, people, and software in your manufacturing facility. Having a strategy in place for making sure all your tools are connected to each other will save you time when it comes time to scale up.
3- Not using machine vision technology
Machine vision can be used in a number of different ways, and it is important to use the right tool for the job. It may be overkill to use machine vision where other types of automation would suffice, but it's also possible that you'll fail to see opportunities or solve problems if you don't employ this technology.
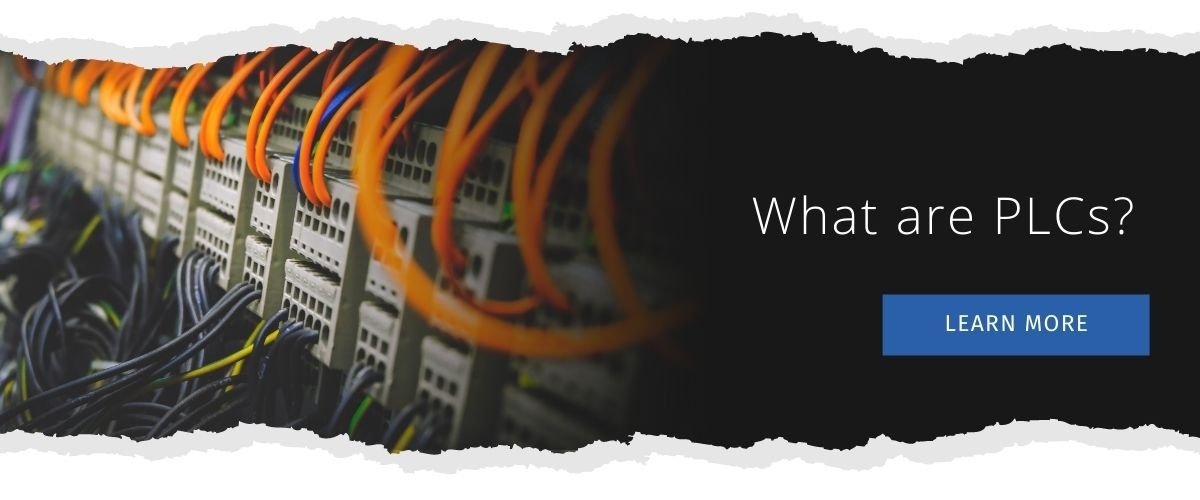
What are some examples of automated machines?
Since there are so many types of equipment used throughout a factory, it's hard to give specific examples of the various ways that automation can be used. Nonetheless, here are some general examples to get you started.
Robotics
Robots are used for tasks that are too dangerous for humans, too precise in nature, or must compete with manual labor costs. Often these robots require machine vision technology and EOATs in order to operate successfully due to the precision required.
Advanced software tools
Advanced software tools are used to ensure that automated machines are able to communicate with the people running them, are able to work efficiently, are able to anticipate changes in demand, and can create error-free work.
Machine vision technology
Machine vision technology is often paired up with robots because it allows for better precision when handling materials or guiding the tools to do their job. Machine vision can also be used with other types of automation and will be the key to most successful automated factories in the future.
Machine retrofitting and Computer numeric control (CNC) machines
Machine retrofitting is the process of using existing equipment in automated systems. The process of machine retroffiting, tends to be difficult with older machines, but many manufacturers are now discovering that it's possible - and cost-effective - to use their legacy equipment in new ways.
Computer numeric control (CNC) machines are becoming more sophisticated as technology advances, allowing them to do tasks that many believed were too difficult for automation. These systems are not quite as flexible as other types of automation, but they can be used to great effect when paired with the right software tools.
Additive manufacturing (AM) and computer-aided design (CAD)
Additive manufacturing (AM) and computer-aided design (CAD) are becoming more prevalent in factories across the world due to their flexibility and potential for large-scale production. AM is already beginning to find a permanent place in a number of factories, and will soon become an integral part of many others as the technology continues to advance.
Automation, Machine Design, and IoT
What is the factory of the future?
A smart factory, or the factory of the future, is automated and designed with computer-guided machinery. When you combine these two factors, it becomes possible to create a smart factory that runs at optimal efficiency levels while meeting all kinds of different kinds of needs.
How do automation, machine design, and IoT combine?
A smart factory is one that relies heavily on the use of automation and machine design in order to become more efficient. The Internet of Things (IoT) represents a new way for industry professionals to communicate with each other, making it easier than ever before for these machines to work together and do their jobs correctly.
Automation and machine design go hand-in-hand when it comes to creating a smart factory, and they are both necessary for the success of an automated future. With the right combination of software tools, machinery, and people, it is possible to create a thriving automated factory that will be able to provide all sorts of different products at a low cost without sacrificing quality.
What happens when automation, machine design, and IoT combine?
When it comes to automation in manufacturing, an automated factory is a vast improvement over any other type of manufacturing process, and when you pair that with the power of IoT it becomes even better.
An efficient smart factory will be able to produce all kinds of products in a cost-effective manner while holding true to modern standards in terms of quality. The future for engineering industries and professionals looks bright thanks to the combination of automation, machine design, and IoT.
Do you have a machine that needs to be automated?
At Nevatio Engineering we know how to build machines and we know how to automate them. Our team is compressied of manufacturing engineering experts who will work with you every step of the way, from design through installation, so your project is completed on time and within budget.
Automation can help increase productivity by up to 500%. It can also reduce costs by as much as 80% when compared with manual labor. And it’s not just about saving money – automation makes workers safer too! You can rest easy knowing that our experienced engineering team will get your job done right the first time around.
So what are you waiting for? Get started today!
Related Articles
What is Industrial AI and Why Does It Matter to Process Manufacturers? - Lets take a closer look at what you need to know about Industrial AI, including industry 4.0, IoT, machine integration, and automated traceability.
About Nevatio Engineering
Nevatio Engineering is an agile design and engineering consulting team capable of on-demand mechanical and electrical engineering, functional prototyping, engineering documentation, and machine retrofits. We are experts in machine design, special devices, industrial products, jigs and fixtures, plus automation and controls. Our added knowledge in industry design standards such as ASME, ANSI, ISO, NFPA, NEC and BS allows us to quickly integrate our services with your existing standard design processes, keeping your resources free from unnecessary rework.
We specialize in helping industry leaders solve difficult engineering and design problems. Our mission is to empower our clients with the tools and skills necessary to create solutions to their technical problems. With our expertise, clients can address any technical design problems that stand in their way.
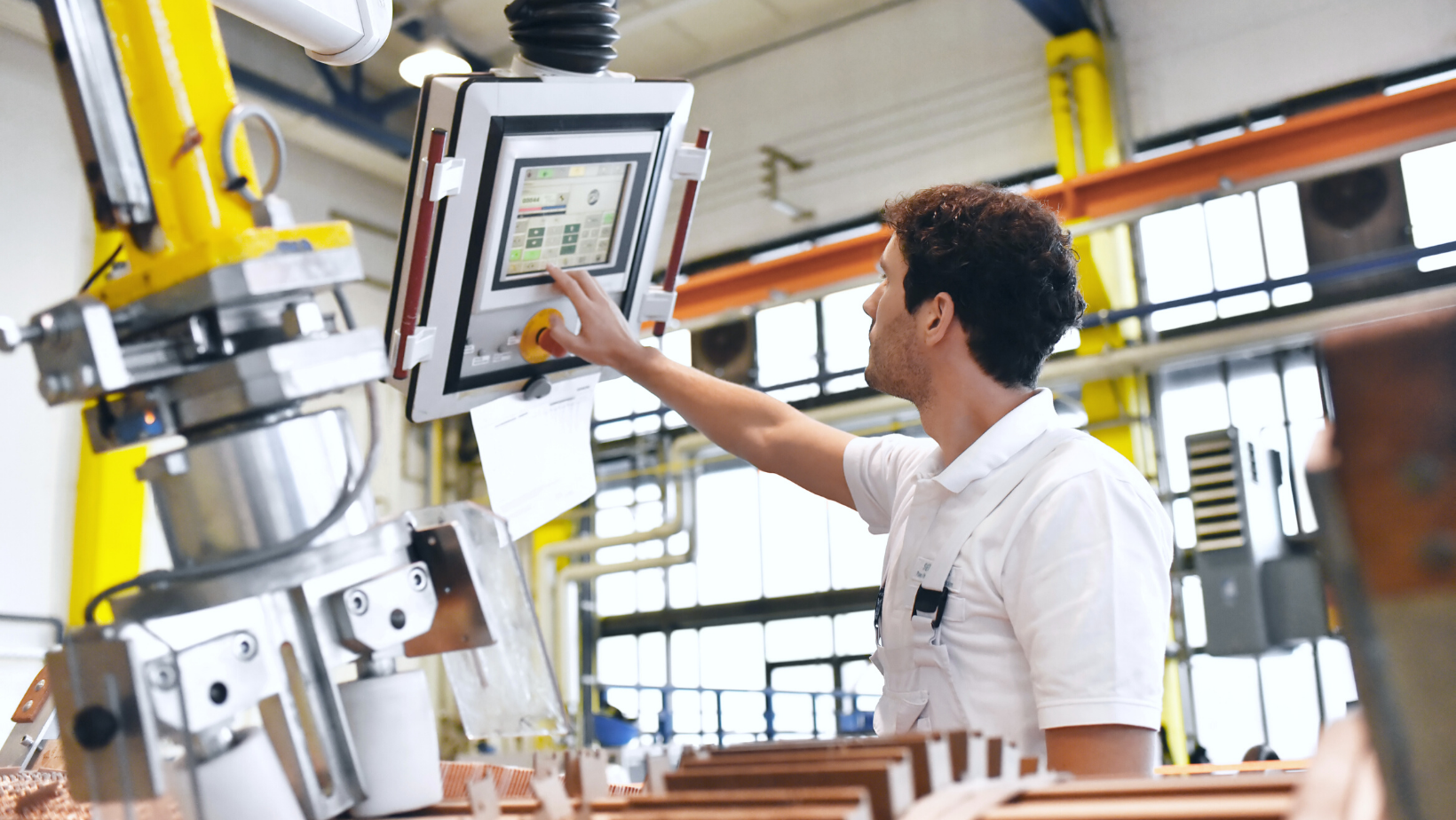
How can simple automation aid manufacturing operators?
Even the most simplistic task can be aided through automation. In manufacturing, operators often have to complete repetitive and time-consuming...
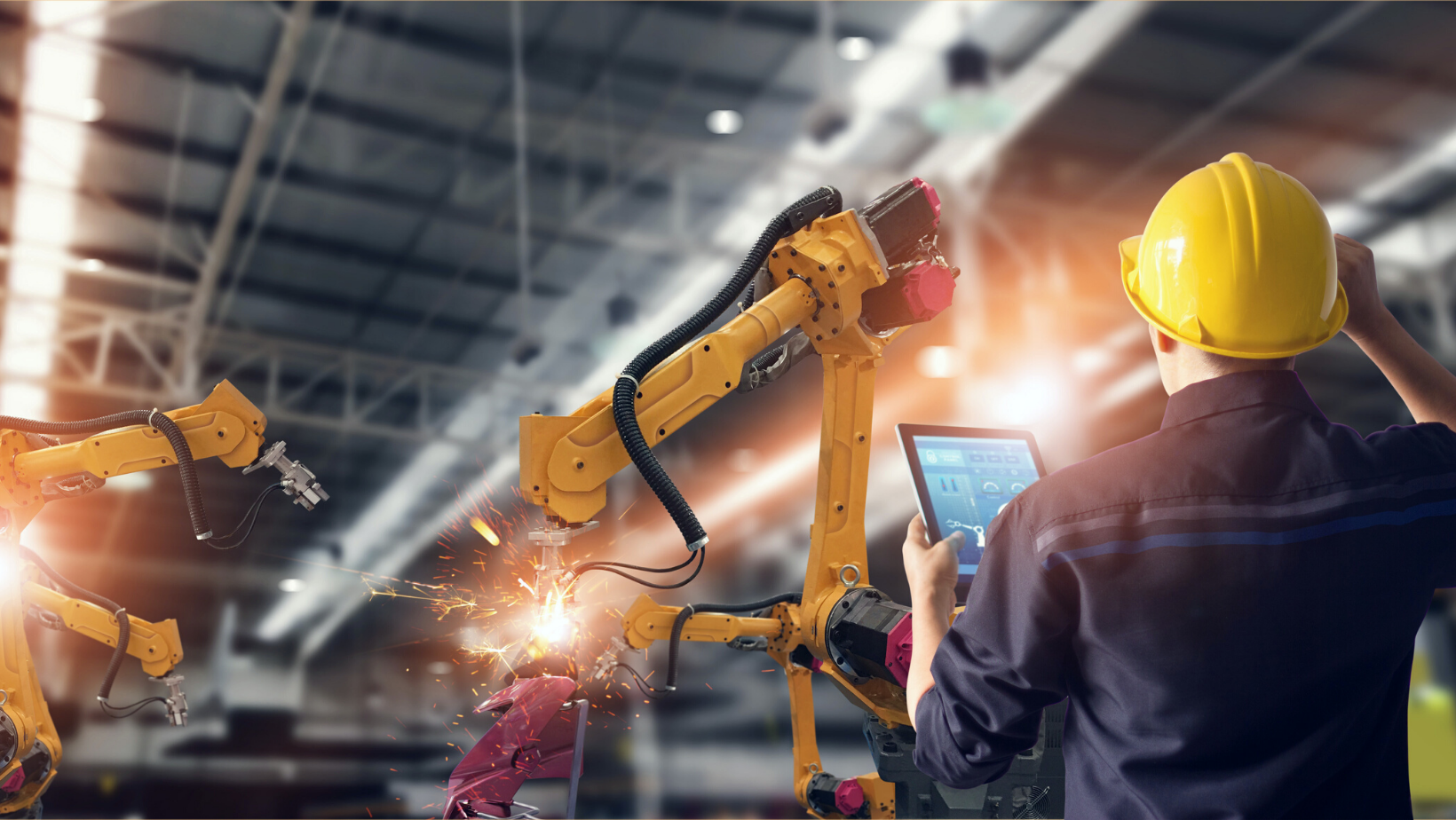
5 Advantages of Industrial Automation
Having industrial automation is a necessity, but there's a lot of gray area when it comes to calculating the benefits. And part of that gray area is...
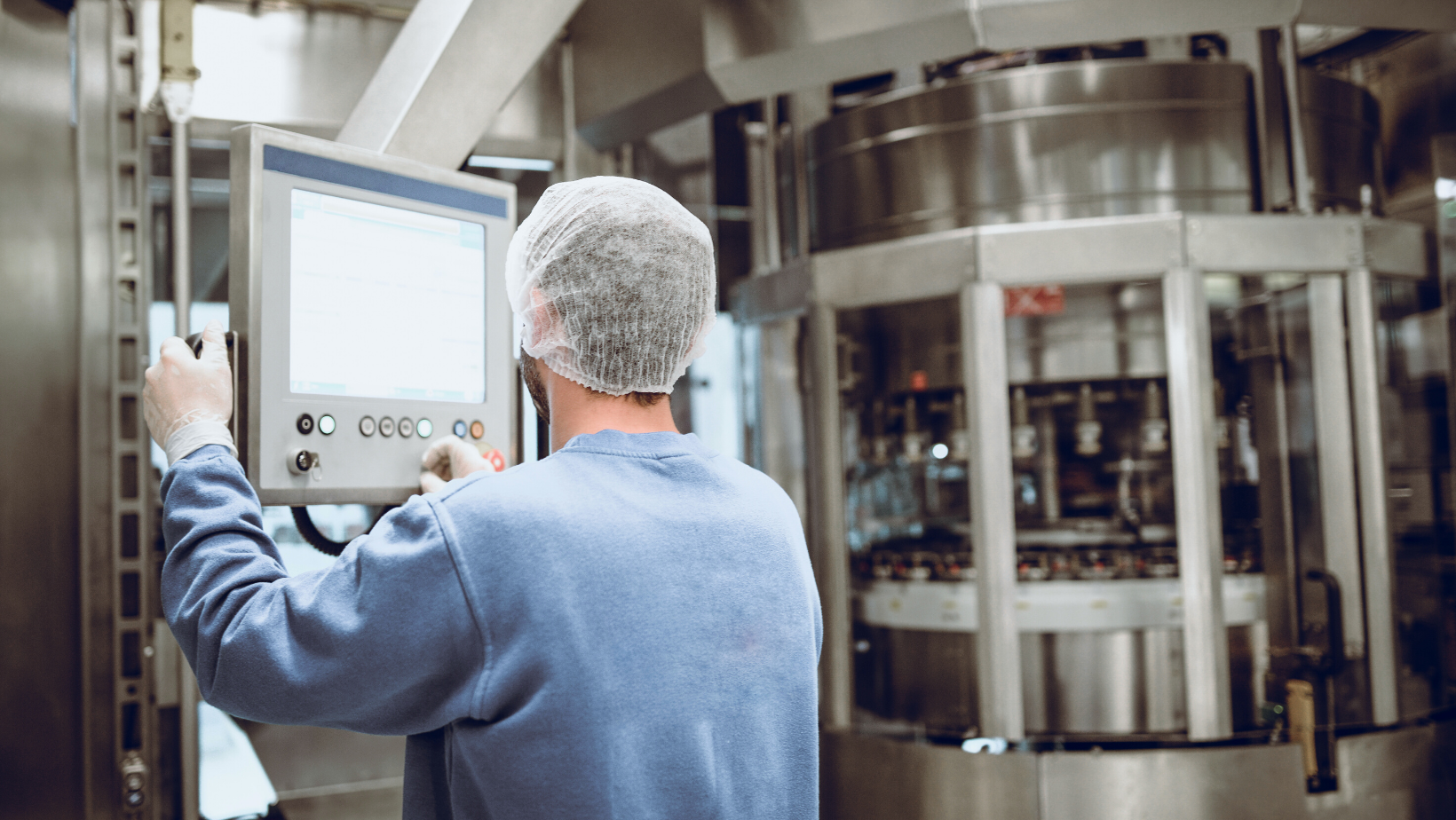
Machine-to-Machine Integration In Manufacturing
As industries move towards the fourth industrial revolution, more and more emphasis is being put on machine-to-machine (M2M) integration. This refers...